The construction industry has seen a significant shift towards energy-efficient, durable, and low-maintenance materials in recent years. Among these materials, PVC (Polyvinyl Chloride) and steel-plastic composite doors and windows have gained popularity due to their superior insulation properties, resistance to weather conditions, and long lifespan. To meet the increasing demand for high-quality products, the machinery used in the manufacturing of PVC and steel-plastic doors and windows has evolved considerably. This article delves into the various types of machinery involved in the production process, as well as the technological advancements that have shaped the industry.
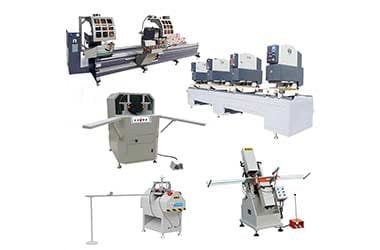
1. Cutting Machines
The profiles need to be cut to specific lengths for the assembly of doors and windows. Cutting machines for PVC and steel-plastic doors and windows are designed to provide precise and clean cuts without damaging the material. These machines typically employ circular saws or high-speed blade systems to cut the profiles with minimal waste.
Modern cutting machines are integrated with computerized numerical control (CNC) systems, allowing for highly precise cuts, reducing errors, and improving production speed. Additionally, some cutting machines are equipped with automatic length measurement and adjustment systems, making them suitable for high-volume production runs.
2. Corner Welding Machines
One of the key steps in assembling PVC and steel-plastic windows and doors is the welding of the profile corners. Corner welding machines are designed to join the profiles at the correct angle (typically 90 degrees) using heat and pressure. This ensures that the frame is strong and leak-proof, essential for the structural integrity and energy efficiency of the final product.
Advanced corner welding machines offer precise control over welding time, temperature, and pressure, ensuring high-quality welds. Some models also feature automatic positioning systems to handle various profile sizes and shapes, further enhancing production efficiency.
3. Cleaning and Milling Machines
Once the profiles are welded together, they need to be cleaned and milled to remove excess material and sharp edges. Cleaning machines help remove any residual PVC or steel, ensuring that the frames are smooth and free from contaminants.
Milling machines are used to create channels for hardware installation, including locks, hinges, and other components. They are also essential for routing out areas for double-glazed units in the frames. Milling machines for PVC and steel-plastic windows are highly accurate and can perform multiple tasks in a single operation, streamlining the manufacturing process.
4. Glazing Machines
Glazing, or the installation of glass units into the frames, is another critical step in the production of windows and doors. Glazing machines are used to insert glass panes into the profiles efficiently and securely. These machines are designed to handle both single and double-glazed units and can apply gaskets or seals to ensure proper insulation.
Modern glazing machines are equipped with vacuum systems, ensuring precise handling of large or heavy glass panels without damage. These machines can also be programmed to handle various sizes of windows and doors, improving flexibility and reducing setup times.
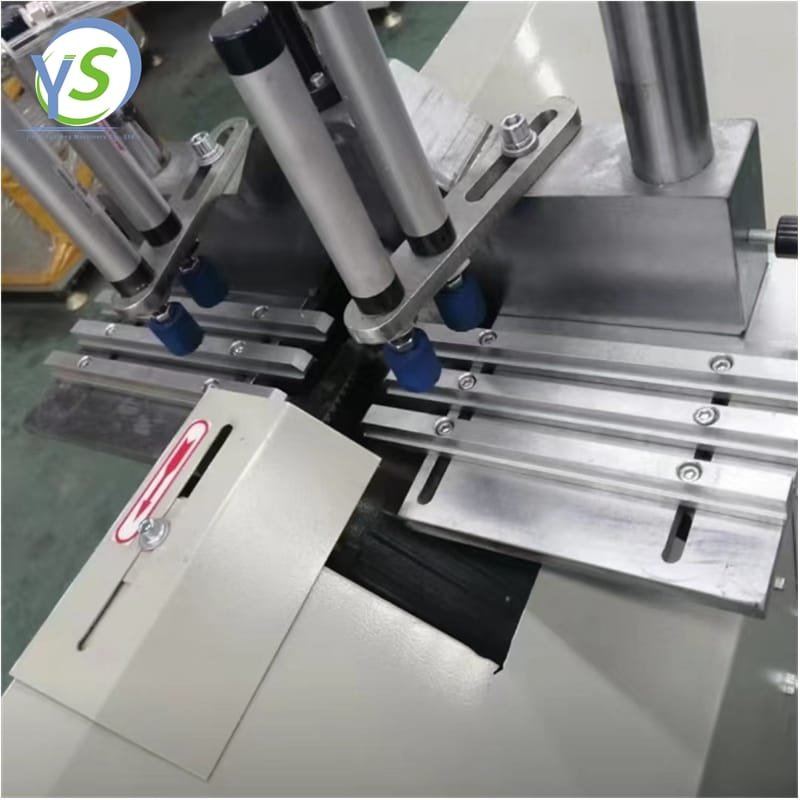
5. Assembly and Testing Lines
Once the individual components have been manufactured, they need to be assembled into complete doors and windows. Assembly lines are designed to bring together all the parts—frame, sash, glass, and hardware—into the final product. Automated assembly lines are increasingly used to enhance speed and reduce the labor force required for assembly.
Additionally, testing equipment is essential to ensure the quality of the finished product. Testing machines check for various parameters such as strength, thermal insulation, air tightness, and water resistance. These systems help ensure that the final product meets industry standards and customer expectations.
6. Technological Advancements in Machinery
The machinery used in the production of PVC and steel-plastic doors and windows has undergone significant technological advancements over the years. Some notable trends include:
- Energy Efficiency: Newer machines are designed to be energy-efficient, consuming less power while maintaining high productivity levels. This is an essential consideration in an era of rising energy costs and environmental awareness.
- Precision and Flexibility: Modern machinery offers higher levels of precision, allowing manufacturers to produce custom-sized and designed doors and windows with ease. CNC-controlled machines enable quick changes to the production setup, allowing for more flexible manufacturing processes.
- Environmentally Friendly Materials and Processes: As sustainability becomes increasingly important, machinery manufacturers are also developing systems to handle eco-friendly materials and minimize waste in the production process.
Conclusion
The machinery used in the production of PVC and steel-plastic windows and doors has evolved rapidly, enabling manufacturers to produce high-quality, energy-efficient, and durable products at competitive prices. From extrusion to glazing, each piece of equipment plays a vital role in the manufacturing process. With the continuous advancements in automation, precision, and sustainability, the future of PVC and steel-plastic door and window production looks promising, meeting the growing demands of the construction industry while also contributing to a more sustainable environment.