In the realm of modern architecture, aluminum alloy door and window systems have emerged as a preferred choice due to their combination of aesthetic appeal, durability, and energy efficiency. Behind the sleek designs and robust performance of these installations lie sophisticated manufacturing equipment that ensure precision, quality, and scalability. This article delves into the world of aluminum alloy door and window equipment, highlighting the key components, technological advancements, and their significance in the construction industry.
**1. Cutting and Machining Equipment
The journey of an aluminum alloy door or window begins with precision cutting. High-tech CNC (Computer Numerical Control) machines play a pivotal role here. These advanced machines utilize computer programs to cut aluminum profiles with exceptional accuracy, ensuring that each piece fits perfectly within the overall design. They can handle complex shapes and intricate patterns, catering to the diverse aesthetic demands of architects and designers.
**2. Punching and Drilling Machines
Once cut, the profiles require holes for fasteners, hinges, and other hardware components. Punching and drilling machines, often automated, efficiently create these openings. These machines guarantee consistent hole sizes and placements, which are crucial for the structural integrity and smooth operation of the doors and windows.
**3. Bending and Forming Equipment
Aluminum alloy doors and windows often feature curved or angled profiles that add to their visual appeal and functional versatility. Bending and forming equipment, such as press brakes and bending rolls, are employed to shape the profiles into the desired contours without compromising their structural strength.
**4. Welding and Joining Technologies
To achieve seamless constructions, welding plays a crucial role.TIG (Tungsten Inert Gas) and MIG (Metal Inert Gas) welding machines are commonly used to fuse aluminum profiles together. These welding processes offer strong, leak-proof joints that can withstand environmental stressors. Additionally, riveting and adhesive bonding technologies are also utilized for specific applications requiring high tensile strength or aesthetic considerations.
**5. Surface Treatment Equipment
Aluminum alloy doors and windows are renowned for their finishes, ranging from sleek anodized coatings to vibrant powder coatings. Surface treatment equipment, including anodizing plants and powder coating booths, applies these protective and decorative layers. These processes not only enhance the visual appeal but also improve corrosion resistance and durability.
**6. Automated Assembly Lines
To meet the high demand for aluminum alloy door and window systems, automated assembly lines have become indispensable. These lines integrate various manufacturing steps, from cutting to assembly, reducing manual intervention and enhancing productivity. Sensors, robots, and conveyors work in tandem to ensure consistent quality and minimize errors.
**7. Quality Control and Testing Equipment
Ensuring the reliability and performance of aluminum alloy doors and windows necessitates rigorous quality control. Testing equipment, such as strength testers, weathering chambers, and soundproofing testers, evaluate the durability, weather resistance, and acoustic properties of the products. These tests guarantee compliance with international standards and customer specifications.
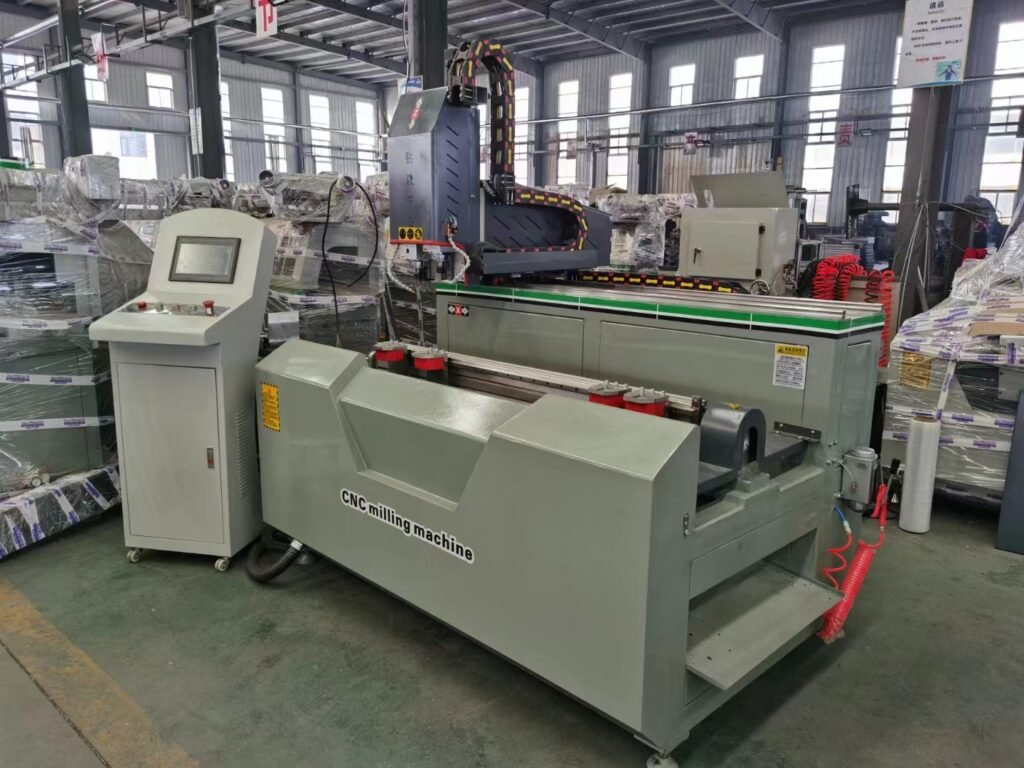
Conclusion
The evolution of aluminum alloy door and window equipment reflects the fusion of advanced technology and innovative design principles. By leveraging precision machinery, automated processes, and rigorous quality control measures, manufacturers are able to produce high-performance, aesthetically pleasing products that meet the diverse needs of the modern construction industry. As technology continues to advance, the capabilities of these equipment will undoubtedly expand, driving further innovations in aluminum alloy door and window manufacturing.