The CNC Drilling and Milling Machine for Aluminum Profiles is an advanced, high-precision machining solution designed specifically for processing aluminum profiles used in various industries such as construction, automotive, aerospace, and electronics. Combining drilling and milling functions into one integrated system, this machine enhances productivity, reduces production costs, and ensures high-quality finished products.
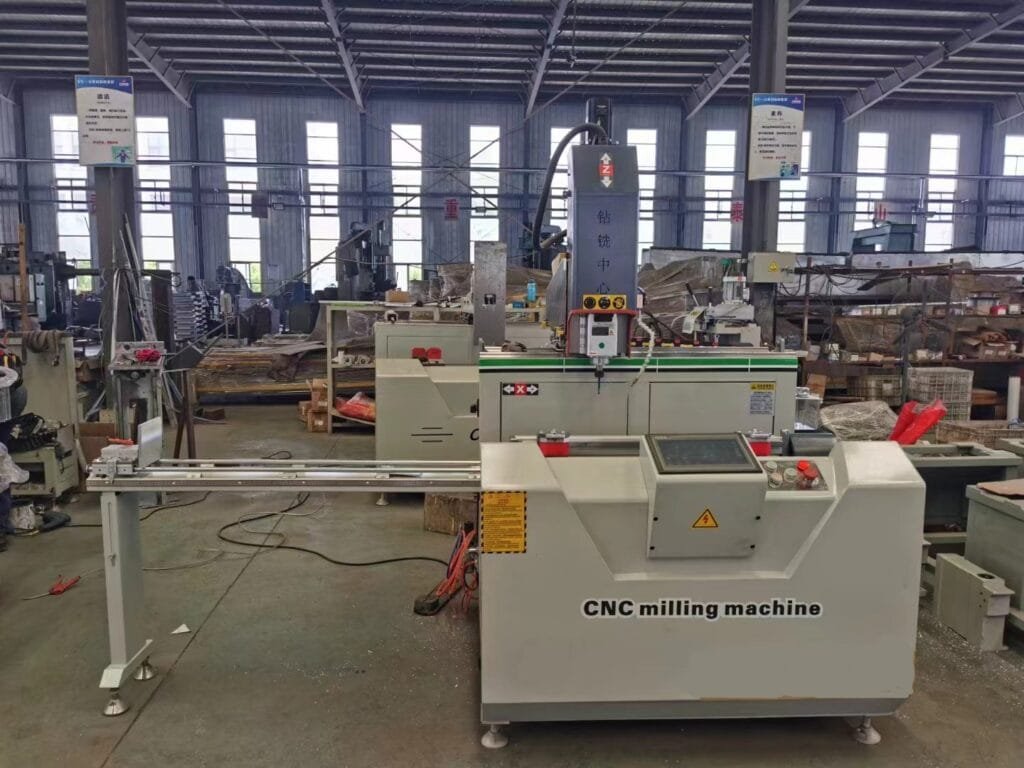
Key Features and Advantages:
- High Precision and Efficiency: The CNC machine is equipped with state-of-the-art technology that ensures precise positioning and accurate machining, reducing the risk of human error. With automated control and real-time monitoring, it delivers consistent results across multiple operations, increasing both productivity and quality.
- Versatility: This machine supports a variety of processes, including drilling, milling, tapping, and countersinking, making it highly versatile for a wide range of applications. It can easily handle different types of aluminum profiles, whether small or large, and adapt to various product shapes and sizes.
- Multi-axis Control: With its multi-axis control system, the CNC machine allows for complex machining tasks to be performed with ease. It can handle multi-dimensional drilling and milling operations without the need for repositioning the workpiece, ensuring faster turnaround times.
- User-Friendly Interface: The CNC system comes with an intuitive, user-friendly interface that simplifies operation and reduces setup times. Operators can easily program the machine through graphical and code-based methods, while pre-programmed routines and a robust library of machining operations enhance ease of use.
- Durability and Reliability: Built with high-quality materials, the machine is designed for long-term operation under demanding conditions. Its robust construction ensures stability, while high-end components reduce wear and tear, resulting in a longer service life and reduced maintenance costs.
- Reduced Human Labor: By automating the drilling and milling processes, this machine significantly reduces the need for manual labor, streamlining production workflows. It can work continuously with minimal downtime, enabling businesses to achieve higher throughput and reduce labor costs.
- Customization and Flexibility: The machine can be customized to meet specific production needs, allowing for adjustments to drilling and milling parameters. Its modular design accommodates various tooling options and fixture configurations, providing flexibility for different machining tasks.
- Cost-Effective: The combination of drilling and milling operations in one machine eliminates the need for multiple separate machines, reducing the overall equipment investment. Additionally, its high efficiency and reduced operational costs translate into significant long-term savings for manufacturers.
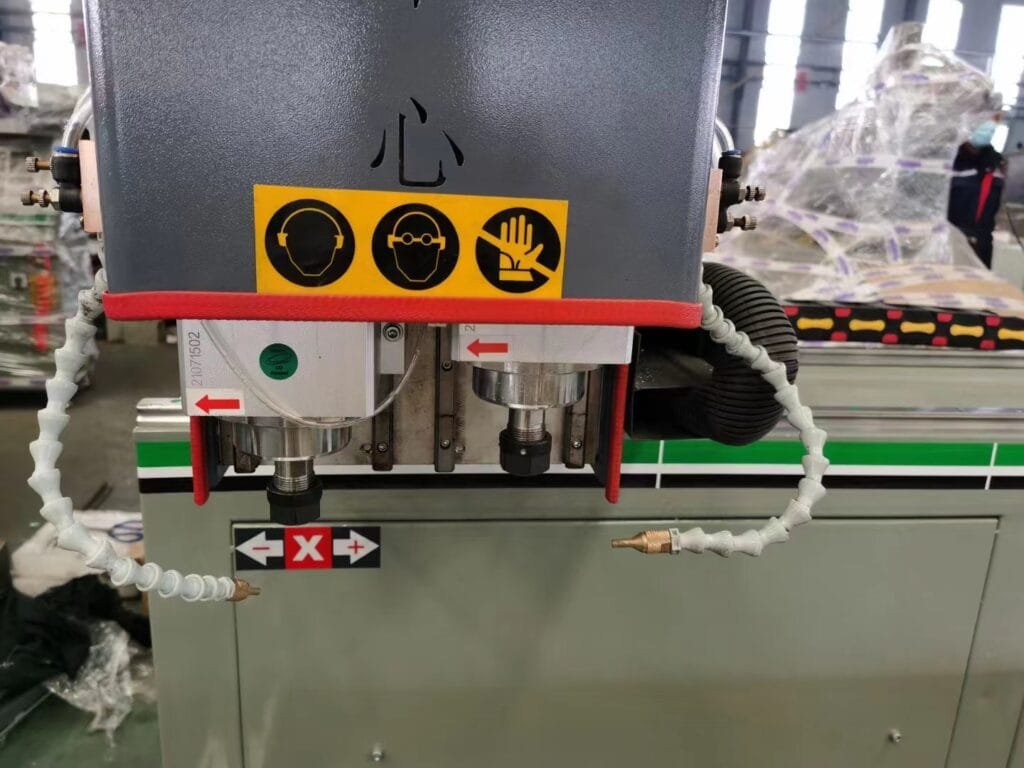
Applications:
The CNC Drilling and Milling Machine for Aluminum Profiles is widely used in the production of products such as:
- Window and door frames
- Curtain wall profiles
- Automotive components
- Heat exchangers and radiators
- Aerospace components
- Electronic housings and enclosures
Conclusion:
In summary, the CNC Drilling and Milling Machine for Aluminum Profiles is a powerful, reliable, and cost-effective solution for manufacturers looking to streamline their production processes. Its ability to perform both drilling and milling operations on aluminum profiles makes it a crucial asset for industries requiring high-precision machining. With its advanced features, ease of use, and versatility, it is an ideal choice for enhancing operational efficiency and product quality.