In the realm of modern manufacturing, precision and efficiency are paramount. Among the myriad of machines that cater to these demands, industrial aluminum cutting machines stand out prominently, especially in the fabrication of aluminum components for diverse applications ranging from aerospace to automotive, electronics, and construction. These machines offer a multitude of advantages that make them indispensable tools in today’s advanced manufacturing landscape. Below are some key benefits of utilizing industrial aluminum cutting machines.
1. High Precision and Accuracy
One of the most significant advantages of industrial aluminum cutting machines is their exceptional precision and accuracy. Equipped with advanced cutting technologies such as laser, waterjet, and plasma cutting, these machines can achieve tolerances that are unattainable by traditional methods. This high degree of precision ensures that parts fit together seamlessly, reducing waste and enhancing the overall quality of the final product.
2. Enhanced Productivity
Industrial aluminum cutting machines significantly boost productivity. Automated processes allow for continuous cutting operations with minimal human intervention, thereby缩短production cycles and increasing output. Furthermore, many of these machines are designed to handle multiple tasks simultaneously, further enhancing their efficiency. This heightened productivity not only meets but often exceeds market demands, enabling manufacturers to stay competitive in fast-paced industries.
3. Versatility in Material Handling
Aluminum, known for its lightweight yet strong characteristics, comes in various grades and thicknesses. Industrial cutting machines are versatile enough to handle a wide range of aluminum alloys, thicknesses, and sizes. Whether it’s sheet metal, extrusions, or custom profiles, these machines can adapt to different materials without compromising on cutting quality. This versatility makes them ideal for producing a diverse range of components tailored to specific industry needs.
4. Cost-Effectiveness
While the initial investment in industrial aluminum cutting machines may be substantial, their long-term cost-effectiveness is undeniable. Reduced waste due to precision cutting, minimized downtime through automation, and the ability to handle complex designs without additional tooling costs all contribute to lower operational expenses. Moreover, the machines’ longevity and durability ensure a favorable return on investment over time.
5. Safety and Reliability
Safety is paramount in any manufacturing environment. Industrial aluminum cutting machines incorporate robust safety features, such as emergency stop buttons, enclosures to protect operators from flying debris, and automated processes that minimize human exposure to hazards. Their reliability stems from advanced controls and sensors that monitor cutting conditions, ensuring consistent results and minimizing the risk of errors. This combination of safety and reliability fosters a secure and efficient workplace.
6. Flexibility in Design and Customization
The digital integration of industrial aluminum cutting machines allows for unparalleled flexibility in design and customization. CAD/CAM software can be seamlessly integrated, enabling manufacturers to design and cut intricate patterns, logos, and geometries with ease. This capability is crucial for industries that require bespoke solutions, enabling rapid prototyping and the production of unique components tailored to specific customer requirements.
7. Environmental Efficiency
Many modern industrial aluminum cutting machines are designed with environmental efficiency in mind. Techniques like dry cutting, which minimizes the use of cutting fluids, and advanced dust collection systems reduce waste and emissions. This commitment to sustainability aligns with the increasing demand for eco-friendly manufacturing practices.
In conclusion, industrial aluminum cutting machines represent a pivotal advancement in modern manufacturing. Their precision, productivity, versatility, cost-effectiveness, safety, design flexibility, and environmental efficiency make them invaluable assets for any business involved in aluminum fabrication. As technology continues to evolve, these machines will undoubtedly play an even more critical role in shaping the future of manufacturing excellence.
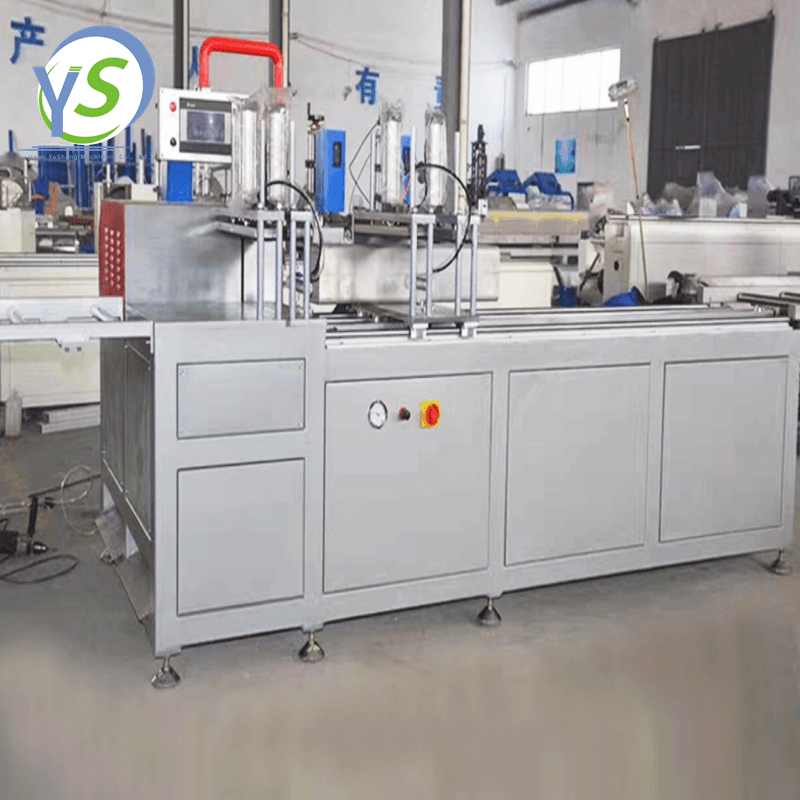