In the realm of metalworking, the aluminum alloy bending machine stands as a testament to technological advancement, blending precision, efficiency, and versatility in a single, robust package. Designed specifically for shaping aluminum alloy materials, these machines have revolutionized the manufacturing industry by offering a suite of features that cater to diverse fabrication needs. Below, we delve into the compelling selling points of aluminum alloy bending machines, highlighting why they are indispensable assets for any metal fabrication shop.
**1. Precision Bending for Flawless Results
At the heart of every aluminum alloy bending machine lies its unparalleled precision. Equipped with advanced control systems and sensors, these machines ensure that every bend is executed with millimeter-perfect accuracy. This level of precision is crucial in industries where aesthetics and functionality are paramount, such as automotive, aerospace, and architectural applications. The ability to produce consistent, defect-free bends enhances the overall quality of the final product, meeting even the most stringent specifications.
**2. Enhanced Productivity and Efficiency
Time is money, and aluminum alloy bending machines understand this all too well. By automating the bending process, these machines significantly reduce setup times and cycle durations, leading to increased productivity. Operators can program complex bending sequences with ease, allowing the machine to run unattended for extended periods. This not only boosts output but also minimizes labor costs, making it an economically viable solution for high-volume production runs.
**3. Versatility Across Various Applications
One of the most appealing aspects of aluminum alloy bending machines is their versatility. Capable of handling a wide range of aluminum alloy thicknesses and grades, these machines can be adapted for different bending radii and angles. From intricate automotive parts to expansive architectural facades, the versatility of these machines ensures they remain a valuable asset across diverse industries. Moreover, with optional accessories and modular designs, they can be easily upgraded to accommodate new or specialized bending requirements.
**4. Material Savings and Cost Reduction
Waste reduction is a critical concern in metal fabrication, and aluminum alloy bending machines deliver on this front. The precision control over bending operations minimizes material scraps and rejections, optimizing material usage. This not only reduces raw material costs but also enhances sustainability by minimizing waste. Additionally, the machines’ ability to handle a variety of alloys without compromising on quality further contributes to cost savings by eliminating the need for secondary operations or replacements.
**5. User-Friendly Operation and Maintenance
Despite their sophisticated capabilities, aluminum alloy bending machines are designed for user-friendly operation. Intuitive control panels and software interfaces make it easy for operators of all skill levels to program and monitor bending processes. Training requirements are minimal, enabling quick adoption and integration into existing workflows. Maintenance is equally straightforward, with easily accessible components and comprehensive service support ensuring downtime is kept to a minimum.
**6. Safety and Compliance
Safety is paramount in any industrial setting, and aluminum alloy bending machines adhere to the highest safety standards. Incorporating features such as emergency stop buttons, safety guards, and automated cycle monitoring, these machines ensure operators remain protected throughout the bending process. Compliance with international safety regulations and certifications further reinforces their credibility and suitability for use in regulated environments.
In conclusion, aluminum alloy bending machines are a cornerstone of modern metal fabrication, offering a blend of precision, efficiency, versatility, and cost-effectiveness that is unmatched by traditional bending methods. Their ability to cater to diverse industries and applications, coupled with user-friendly operation and robust safety features, makes them an invaluable investment for any business looking to elevate its fabrication capabilities. As technology continues to evolve, aluminum alloy bending machines will undoubtedly play an even more pivotal role in shaping the future of metalworking.
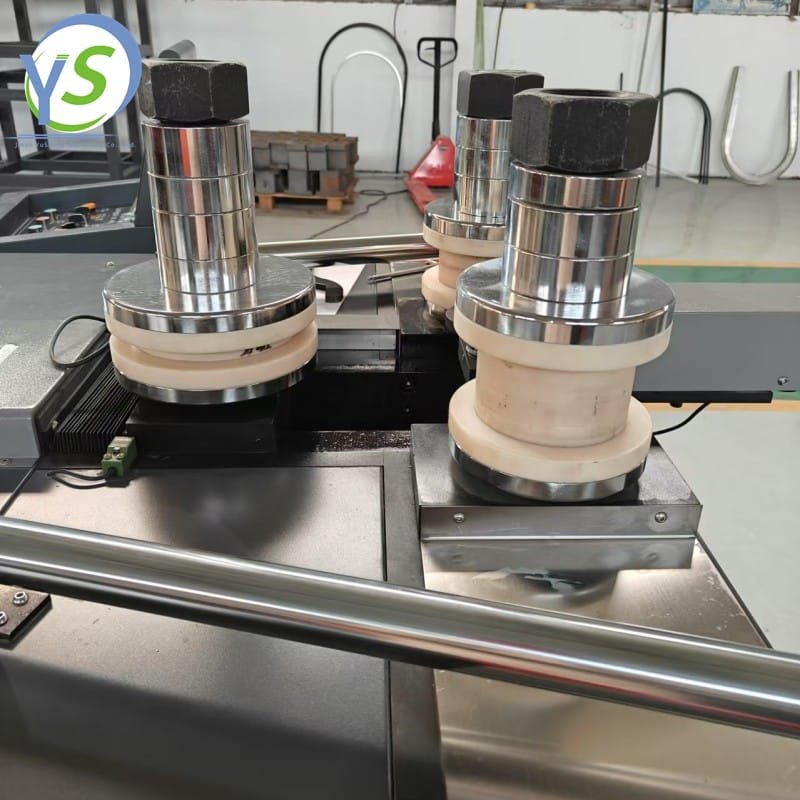